Basic Info.
Model NO.
CVW-8050
Touch Screen
Touch Screen
Sorting Method
Pusher-bar
Transport Package
Strong Ploywoodencase
Specification
2cbm
Trademark
vikingdetector
Origin
Made in China
HS Code
8543709100
Production Capacity
50 Pieces/Weeek
Product Description
**Optimizing Operations: Belt Drive Conveyor Checkweighing in Manufacturing and Shipping Facilities**
In manufacturing and shipping facilities, precision in weighing and sorting processes is paramount to ensure product quality and compliance with shipping standards. Belt Drive Conveyor Checkweighing systems play a crucial role in these operations, providing an efficient and automated solution for accurate weight verification. This article explores the significance of Belt Drive Conveyor Checkweighing, its key features, applications, and how it contributes to streamlined processes in manufacturing and shipping.
**I. Introduction to Belt Drive Conveyor Checkweighing**
Belt Drive Conveyor Checkweighing is a system designed for automated weight verification of products as they move along a conveyor belt. It integrates a conveyor system with precision checkweighing technology, allowing for real-time weight checks and sorting of products based on specified weight criteria.
**II. Key Features of Belt Drive Conveyor Checkweighing**
1. **Conveyor System:** Utilizes a conveyor belt for the smooth and continuous movement of products through the checkweighing process.
2. **Load Cells:** Incorporates load cells or weighing sensors that measure the weight of products accurately as they pass through the conveyor.
3. **Automated Sorting:** Includes a sorting mechanism to divert products that deviate from specified weight criteria to separate lanes or areas.
4. **High-Speed Operation:** Engineered for high-speed production lines, ensuring efficient and real-time weight checks without disrupting the workflow.
5. **User-Friendly Interface:** Equipped with an intuitive interface for easy setup, monitoring, and adjustment of parameters by operators.
**III. Applications in Manufacturing and Shipping Facilities**
1. **Quality Control in Manufacturing:** Verifying the weight of manufactured products to ensure compliance with quality standards before packaging.
2. **Shipping and Distribution:** Checking the weight of packages in shipping facilities to comply with shipping regulations and optimize logistics.
3. **Food and Beverage Industry:** Verifying the weight of packaged food items to meet regulatory requirements and ensure consumer satisfaction.
4. **Pharmaceutical Manufacturing:** Ensuring precise weight in pharmaceutical packaging to comply with regulatory standards and guarantee dosage accuracy.
**IV. Advantages of Belt Drive Conveyor Checkweighing**
1. **Precision and Accuracy:** Ensures precise weighing of products, contributing to the consistency and quality of manufactured goods.
2. **Efficiency in Production:** Optimizes production processes by conducting weight verifications in real-time at high speeds.
3. **Compliance with Regulations:** Meets industry standards and regulatory requirements for product weight, preventing legal and financial repercussions.
4. **Reduced Product Waste:** Minimizes product waste by promptly identifying and sorting items that deviate from specified weight criteria.
**V. Challenges and Considerations**
1. **Integration with Existing Systems:** Ensuring seamless integration with existing production and conveyor systems.
2. **Calibration and Maintenance:** Regular calibration and maintenance to uphold the accuracy of the weighing components.
**VI. Future Trends and Developments**
The future of Belt Drive Conveyor Checkweighing may involve advancements in connectivity, data analytics, and the integration of artificial intelligence for more adaptive and predictive quality control.
**VII. Conclusion**
Belt Drive Conveyor Checkweighing systems are integral to optimizing operations in manufacturing and shipping facilities. Their ability to conduct real-time weight verifications and automated sorting contributes to the efficiency, accuracy, and compliance of processes. As technology continues to evolve, these systems will likely play an increasingly crucial role in maintaining high standards in production, quality control, and logistics.
A checkweigher, also known as an automated machine that weighs items while they are passing through a production line is commonly used. However, if it isn't appropriate for your line of production it could cause production to be slow or stop altogether. A checkweigher's technical parameters include weighing range, conveying capability, measurement accuracy, scale interval, and measurement accuracy. This paper will explain the basics of a checkweigher.
Metal detector general specification
High Performance Checkweighing for Manufacturers
A high performance checkweigher from Vikingdetector helps prevent underfilled or overfilled packages from reaching consumers. It also reduces product waste and rework time, provides completeness checks for package components and important production data for process improvements.
This helps to keep manufacturers in compliance with local weights and measures regulations as well as industry standards. More importantly, it helps to reduce production costs by reducing wasted product through the use of real-time feedback and automatic adjustment to filling equipment.
The optional Due Diligence Kits add further monitoring options, which make certain non-conforming or defective products are safely removed from the production line. To make rework easier to perform, the system can even sort products into different reject bins depending on the issue.
Suitable for
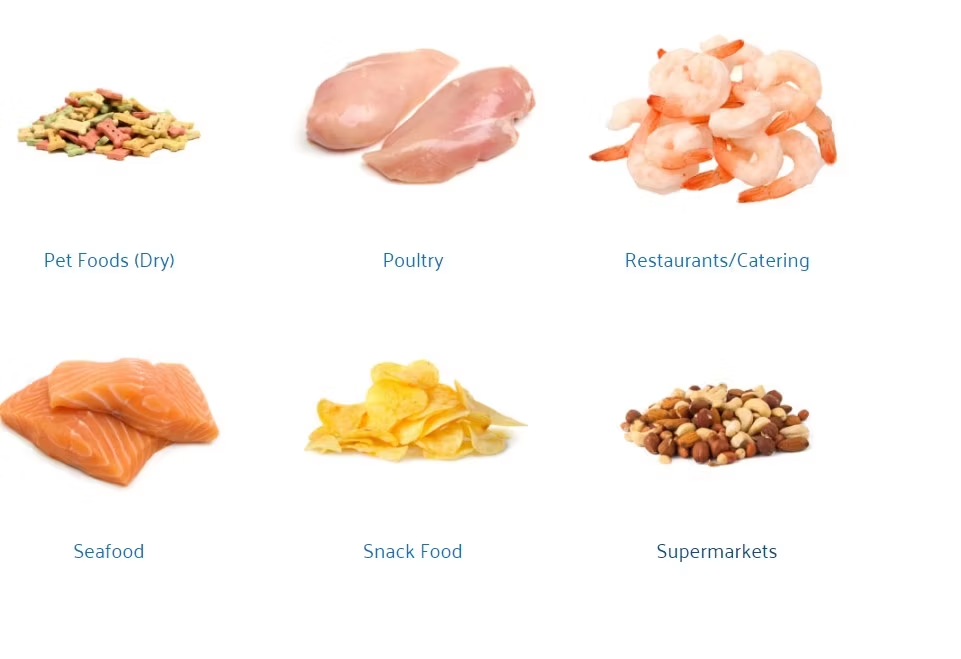
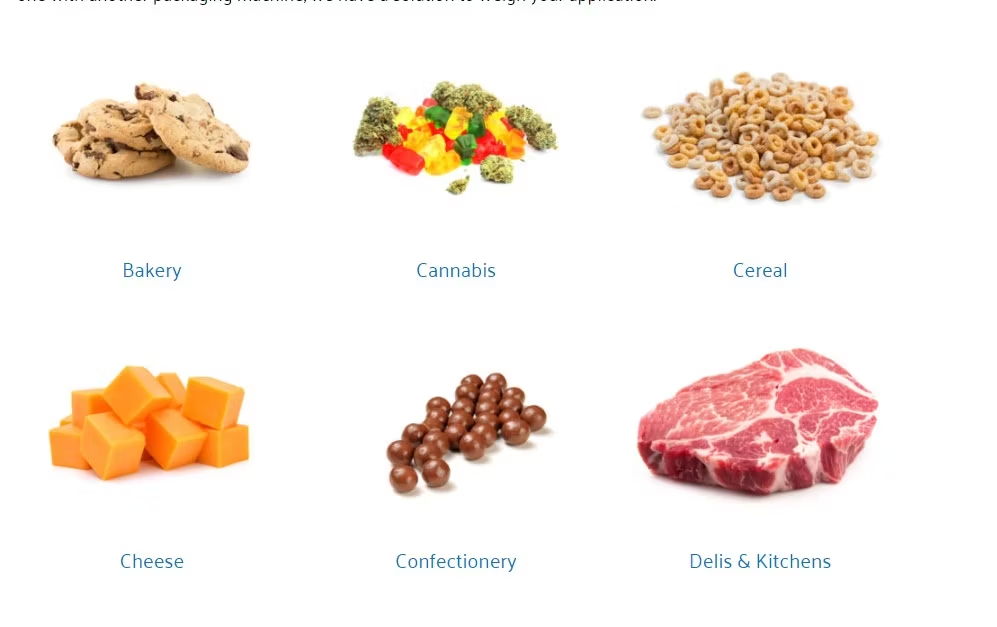
In manufacturing and shipping facilities, precision in weighing and sorting processes is paramount to ensure product quality and compliance with shipping standards. Belt Drive Conveyor Checkweighing systems play a crucial role in these operations, providing an efficient and automated solution for accurate weight verification. This article explores the significance of Belt Drive Conveyor Checkweighing, its key features, applications, and how it contributes to streamlined processes in manufacturing and shipping.
**I. Introduction to Belt Drive Conveyor Checkweighing**
Belt Drive Conveyor Checkweighing is a system designed for automated weight verification of products as they move along a conveyor belt. It integrates a conveyor system with precision checkweighing technology, allowing for real-time weight checks and sorting of products based on specified weight criteria.
**II. Key Features of Belt Drive Conveyor Checkweighing**
1. **Conveyor System:** Utilizes a conveyor belt for the smooth and continuous movement of products through the checkweighing process.
2. **Load Cells:** Incorporates load cells or weighing sensors that measure the weight of products accurately as they pass through the conveyor.
3. **Automated Sorting:** Includes a sorting mechanism to divert products that deviate from specified weight criteria to separate lanes or areas.
4. **High-Speed Operation:** Engineered for high-speed production lines, ensuring efficient and real-time weight checks without disrupting the workflow.
5. **User-Friendly Interface:** Equipped with an intuitive interface for easy setup, monitoring, and adjustment of parameters by operators.
**III. Applications in Manufacturing and Shipping Facilities**
1. **Quality Control in Manufacturing:** Verifying the weight of manufactured products to ensure compliance with quality standards before packaging.
2. **Shipping and Distribution:** Checking the weight of packages in shipping facilities to comply with shipping regulations and optimize logistics.
3. **Food and Beverage Industry:** Verifying the weight of packaged food items to meet regulatory requirements and ensure consumer satisfaction.
4. **Pharmaceutical Manufacturing:** Ensuring precise weight in pharmaceutical packaging to comply with regulatory standards and guarantee dosage accuracy.
**IV. Advantages of Belt Drive Conveyor Checkweighing**
1. **Precision and Accuracy:** Ensures precise weighing of products, contributing to the consistency and quality of manufactured goods.
2. **Efficiency in Production:** Optimizes production processes by conducting weight verifications in real-time at high speeds.
3. **Compliance with Regulations:** Meets industry standards and regulatory requirements for product weight, preventing legal and financial repercussions.
4. **Reduced Product Waste:** Minimizes product waste by promptly identifying and sorting items that deviate from specified weight criteria.
**V. Challenges and Considerations**
1. **Integration with Existing Systems:** Ensuring seamless integration with existing production and conveyor systems.
2. **Calibration and Maintenance:** Regular calibration and maintenance to uphold the accuracy of the weighing components.
**VI. Future Trends and Developments**
The future of Belt Drive Conveyor Checkweighing may involve advancements in connectivity, data analytics, and the integration of artificial intelligence for more adaptive and predictive quality control.
**VII. Conclusion**
Belt Drive Conveyor Checkweighing systems are integral to optimizing operations in manufacturing and shipping facilities. Their ability to conduct real-time weight verifications and automated sorting contributes to the efficiency, accuracy, and compliance of processes. As technology continues to evolve, these systems will likely play an increasingly crucial role in maintaining high standards in production, quality control, and logistics.
A checkweigher, also known as an automated machine that weighs items while they are passing through a production line is commonly used. However, if it isn't appropriate for your line of production it could cause production to be slow or stop altogether. A checkweigher's technical parameters include weighing range, conveying capability, measurement accuracy, scale interval, and measurement accuracy. This paper will explain the basics of a checkweigher.
Precision checkweigher for the food and cosmetic, nutraceutical as well as pharmaceutical and CBD sectors. This highly sensitive, high stable checkweigher allows you to weight-check packaged products to ensure compliance with quality standards.
- Detecting Range : Range 5g - 10kg
- Scale Interval: Range 0.05g - 1g
- Max Speed Range: 105 -250 pcs/min
- Belt Speed: 70m/min
- Weighed Product Size - Width: Range 150 - 390mm
- Product Weight - Length Range: 200 - 500mm
- Weigher Platform Size-Width: Range 160-400mm
- Weigher Platform Size-Length: Range 280 - 650mm
- Stocking of Product: 100
Metal detector general specification
Detected products Height | 80 | 120 | 80 | 100 | 120 | 150 | 200 |
Detected products Width | 300 | 300 | 400 | 400 | 400 | 400 | 400 |
Belt Width | 250 | 250 | 350 | 350 | 350 | 350 | 350 |
Belt length | 1500 | ||||||
Detector sensitivity | Feф0.5 | FeФ0.8 | FeФ0.6 | FeФ0.7 | FeФ0.8 | FeФ0.8 | FeФ1.0 |
SUSф1.0 | SUSФ1.5 | SUSФ1.0 | SUSФ1.2 | SUSФ1.5 | SUSФ2.0 | SUSФ2.3 | |
N-Feф0.8 | N-FeФ1.0 | N-FeФ0.8 | N-FeФ1.0 | N-FeФ1.2 | N-FeФ1.5 | N-FeФ1.5 | |
Speed of belt | 27M/min (can adjust 5-40 M/min) | ||||||
Load ability | 20KG | ||||||
Count | 100 | ||||||
Reject Ways | Sound and light alarm with belt stoped ;(when has auto-reject system ,belt continue and rejecting the goods ) | ||||||
Application | Non-package ,plastic package ,paper bag or box (non-metallic) product | ||||||
Work Environment | Temperature -10ºC-40ºC ,relative humility 30-90% |
High Performance Checkweighing for Manufacturers
A high performance checkweigher from Vikingdetector helps prevent underfilled or overfilled packages from reaching consumers. It also reduces product waste and rework time, provides completeness checks for package components and important production data for process improvements.

Comply with Industry Regulations and Local Weights and Measures
Dynamic checkweighers verify the weight of every product on the line, detecting and remove an underfilled product before it becomes a problem. In addition, the load cells that power our checkweighers are able to filter out environmental noise that could influence the weighing result, meaning a reduction in false rejects.This helps to keep manufacturers in compliance with local weights and measures regulations as well as industry standards. More importantly, it helps to reduce production costs by reducing wasted product through the use of real-time feedback and automatic adjustment to filling equipment.
The optional Due Diligence Kits add further monitoring options, which make certain non-conforming or defective products are safely removed from the production line. To make rework easier to perform, the system can even sort products into different reject bins depending on the issue.
Throughput | Max180 ppm |
Belt speed | 20-60m/min |
Weighing Range | ≤200g |
Suitable Product Dimension | ≤100mm(L)*100mm(W) |
Weighting section | 250mm(L)*120mm(W) |
Transport Height | 550 mm - 1,100 mm (± 50 mm)Customized |
Industry | Food; Other |
Mini resolution | 0.01g(10mg) |
Accuracy | ±0.05g(50mg)~±0.1g(100mg) |
Production Environment | Temperature: 0ºC~40ºC,Humidity:30%~95% |
Operation language | English /Spanish/Russian |
Customization Options | Bespoke handling; OEM |
Approval | Weights & measures design approval for official verification (MID certifiable) If needed |
Suitable for
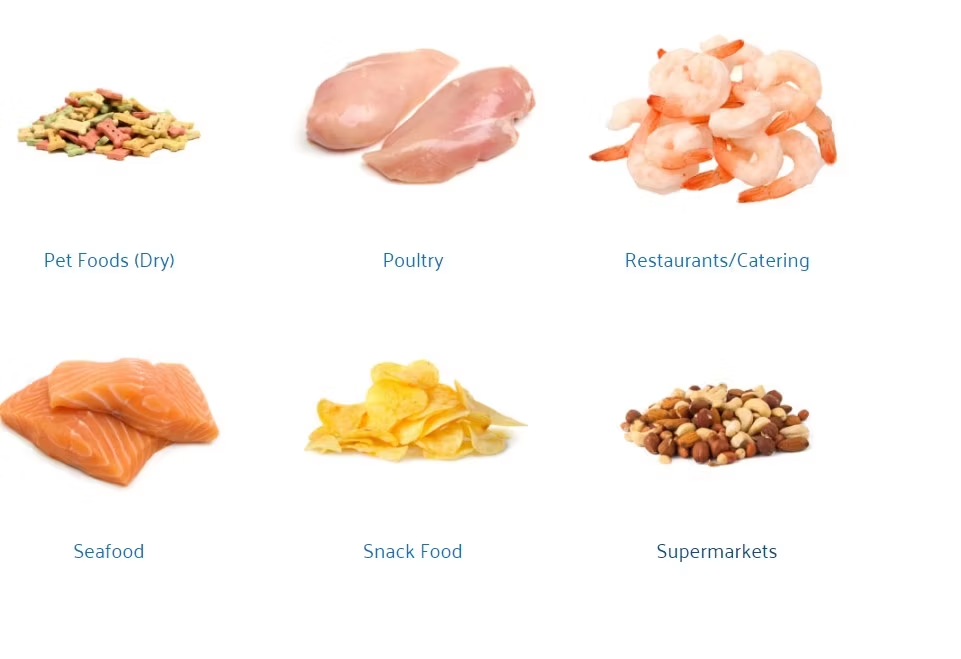
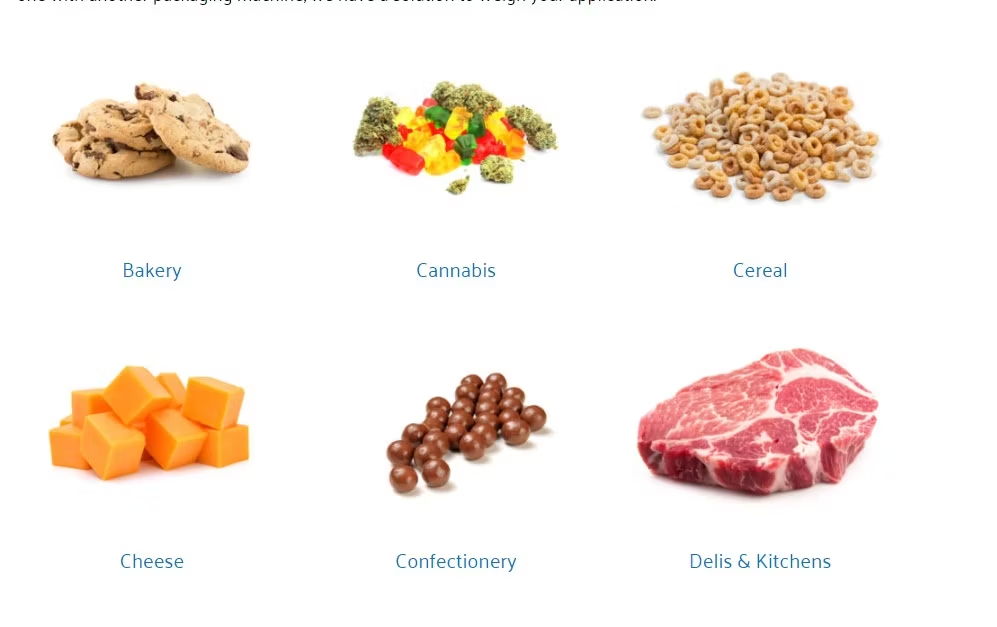

